One of the most fundamental and commonly overlooked aspects of the metal stamping process is the use of the shortest possible stroke for a given application. Many stampers state that they are aware of the importance of this factor, but do not quite understand the benefits behind it.
The Stroke Length Dilemma in Stamping
Too often we hear from customers that they are in search of a press with a longer stroke than what is required for the tooling of a particular application all for the sake of ensuring "flexibility" in their operation. While yes having a longer stroke gives you the capability to run multiple jobs in the same press, stampers tend to not think of the consequences associated with this line of thinking.
In this article, we'll break down some of the main reasons why using the shortest stroke for stamping processes is the best. But first, let's take a look at how stampers are often hurting their bottom line by ignoring this fundamental concept.
The Hidden Costs of Using A Longer Stroke Than Necessary
Using a longer stroke than what is needed can be detrimental in many ways regarding your process. It is important to understand the impact longer strokes can have on your process such as:
- Wasted Time - When using a longer stroke there is a great deal of wasted time and motion in the stroke, which leads to inefficiencies in throughput and quality. More time is spent on the ram traveling to the working portion of the stroke than in the working portion of the stroke.
- Increased Press Wear - Utilizing a longer stroke will have a detrimental effect on the life of your press. If the ram has to travel further than what is necessary there will be additional wear on the guides and the internal structure of the press, which will lead to more frequent maintenance and downtime. As we all know time is money in this industry, and maintenance can sometimes be expensive for mechanical issues.
- Increased Tool & Die Wear - When using a longer stroke there is greater impact velocity when the upper tooling makes contact with the material. High-impact velocities can lead to the tooling either becoming worn much faster than usual or even breaking prematurely. This will lead to more downtime due to waiting for the tooling to be sharpened or replaced, so this not only leads to more expenses for maintaining the press but also for keeping your tools in working shape.
- Decreased Part Quality - With the points above in mind, you will see the quality of the finished parts begin to drop off. More parts will be out of tolerance or not up to the customer standards equals more wasted time, effort, and ultimately money.
While the idea may sound appealing in theory or when looking towards the future expansion of your business, you must keep in mind that there are a great deal of hidden costs. In summary, when you purchase a press with a stroke that is longer than what you need just to obtain added flexibility you must also consider the costs associated with doing so.
Advantages of Using the Shortest Stroke Possible
Using the shortest stroke in your stamping process is one of the simplest ways to improve your operational efficiency. Metal Stampers should understand what they can gain by employing the shortest possible stroke for a given process which includes the following:
- Reduction in Wasted Stroke - By having a reduced stroke there is less wasted motion. These more efficient strokes dedicate more time to forming, which is essential for producing high-quality in-tolerance parts.
For example, consider two presses stamping material at 50 strokes per minute with a thickness of 0.25 inches, one press has a 12-inch stroke and the other uses a 6-inch stroke. The press with a 6-inch stroke notices a 42% increase in forming time over the press with a 12-inch stroke.
- Less Dynamic Forces in the Press - When moving the ram and upper die up and down over a shorter distance in a given amount of time you will see less harmful forces being imparted on the press frame and the drive system. Not only does this impact the drive system and the frame, but it will also preserve the integrity of the guides within the press. This leads to a longer lifespan for the mechanical components and structure of the press, meaning less downtime and maintenance will be required to keep the press performing optimally.
- Increased Effective Tool Life - When you shorten the stroke of your press to only what is needed the upper die has a decreased impact velocity as it makes contact with the material when compared to a longer stroke. The decrease in impact velocity will drastically improve the durability of your tooling and cut down on the occurrence of punches or guides breaking prematurely. This equates to less time and money spent on maintaining and fixing your tools which is another source of downtime.
- When comparing the two strokes the press with the press with the shorter stroke shows a 30% decrease in forming time.
To summarize there are many advantages to utilizing the shortest possible for a given metal stamping application. Not only can you improve the throughput from a more efficient stroke, but you will also see drastic improvements in the life of your tooling and the press itself. These advantages will add more money back to your business's bottom line while also cutting down on the expenses required to maintain your equipment.
The Most Optimal Stroke is Always the Shortest Stroke
Based on the hidden costs of using longer strokes in your process, it is safe to say that it is well worth a company's time and effort to use the shortest possible stroke for a given process. To determine what the shortest stroke possible is for your application you must take the finished part and the time needed for feeding into account. Once these factors are examined you can gain insight into what the shortest stroke needed will be and can respond accordingly.
Sangiacomo Presses Americas is ready to help you optimize your stamping operations with our adjustable stroke press.
Still considering your options? Our team will gladly answer any questions or concerns you may have.
Contact us today at 256-275-4701 or email us at info@sangiacomo-presses.com.
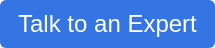