Welcome to the first article in this blog series on Industry 4.0! In this series, we'll address unanswered questions and roadblocks surrounding the term and its implementation in factories or small job shops. We'll tackle the "what, "why", and "how" of Industry 4.0, and why it should matter to machine manufacturers and suppliers alike.
By now, you’ve probably heard of the buzzword humming in your social media, conference rooms, and industry news outlets. You guessed it—“Industry 4.0”. Let's go over this term’s origin, why it’s relevant, and why this latest revolution has been challenging for some to embrace and implement.
In this article titled "Industry 4.0: Manufacturing Then vs. Now", we'll cover the following:
- What is Industry 4.0 and Why is it Relevant?
- Industry 4.0: Then vs. Now
- 4 Obstacles to Embracing Industry 4.0
- Moving Forward with Industry 4.0
What is Industry 4.0 and Why is it Relevant?
Interconnected devices are nowadays commonplace in households with phones, Smart TVs, security cameras, appliances, etc. Thanks to the quick adoption of Industry 4.0 (I4.0) in these industries, the convenience of insight gained from these commonly interconnected devices is done with ease—at least to the common consumer’s eyes. However, if you take a closer look at Industry 4.0 adoption, you’ll see that it’s not so simple after all.
When considering Industry 4.0 adoption, there are big differences between industries. This is especially true for the traditional manufacturing industry. For industrial machinery, the intricacies and risks of implementing two-way communication between machinery and computers are much more apparent. This is in part because our industry is historically characterized by lethargy, risk aversion, and resistance to change.
This helps explain why the adoption of interconnectivity and the use of data has been slower in industry and between different industries. Notoriously, the adoption of Industry 4.0 in traditional manufacturing has been much slower than in modern technologies, such as additive manufacturing, and in logistics or healthcare.
Industry 4.0: Then vs Now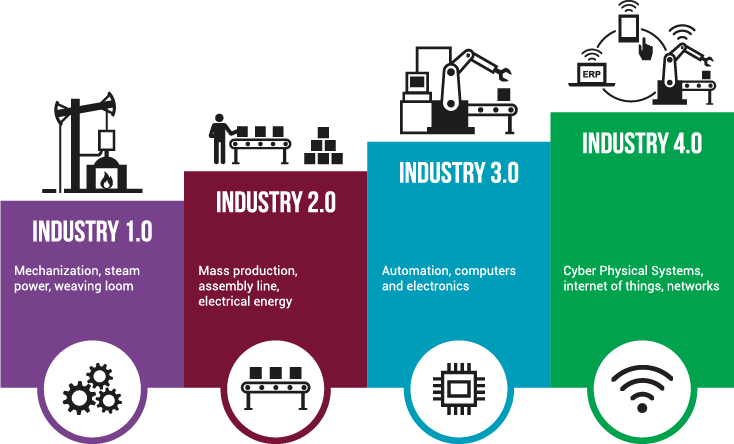
To understand more about the buzzword that’s gotten people talking, let’s go over how we got to Industry 4.0 over centuries of innovation:
Industry 1.0
The first industrial revolution occurred in the mid to late 18th century, when much of the hand labor was replaced by mechanical devices.
Industry 2.0
Near the end of the 19th century, electrification marked the second industrial revolution where mechanical devices were replaced by independently powered machines.
Industry 3.0
The third industrial revolution started in the mid-20th century with the arrival of the programmable logic controller. Automation has radically transformed manufacturing ever since.
Industry 4.0
The fourth and current industrial revolution grew out of an effort launched by the German government to promote the computerization of traditional manufacturing. The aim of the research was to realize a "smart factory" by connecting machines based on the Internet of Things (IoT). The term Industry 4.0 was publicly introduced at the 2011 Hannover Fair to indicate that the use of machine data would radically transform manufacturing like the previous three industrial revolutions.
4 Obstacles to Embracing Industry 4.0
Small-size and even mid-size companies are cautious or struggle with implementing Industry 4.0. Here are four possible obstacles to embracing Industry 4.0:
- Lack of clarity. Companies lack clarity on how to transition to a digital data-driven manufacturing process. In addition, over 850 terms and acronyms are now associated with Industry 4.0 (Fachlexikon MES & Industry 4.0, L. Schleupner, MES D.A.CH Verband e. V). Depending on the industry, equipment manufacturers are equally slow in investing in the technology until it is clear that efforts will help their bottom line or until they're forced to do more. Currently, most of the equipment can be connected to a network which makes them Industry 4.0 ready, but that in itself is useless without software for data exchange.
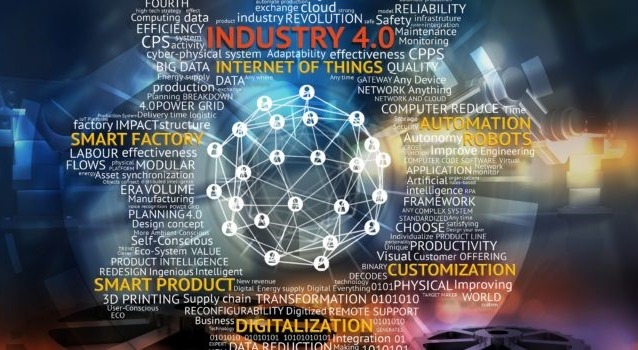
- No established software platform. Without a clear winner, the adoption of a software standard stalls until an established software platform is apparent. Remember in the 1980s when consumers delayed video cassette purchases until there was a declared winner between the VHS (Sony) and Beta Max (Toshiba) formats? Decades later, a similar battle ensued between the HD DVD and Blue Ray formats. A similar situation is at hand here with the adoption of I4.0.
- Security and financial risks. Data exchange software and networked machines require proper security and network maintenance to prevent havoc caused by hackers, automatic updates, malware, and outages. Most companies cannot handle such an IT burden.
- Reluctant company culture and management. Many factors are at play here, but risk-aversion in company culture and management is one reason that some companies are not willing to embrace a revolutionary change or let data speak. On one hand, it may be due to an inherent resistance to change, or fear about what the data may reveal. In most cases, though, it's an uncomfortable truth that keeps them from embracing change. However, that is exactly the fundamental driver of Industry 4.0— the removal of human biases and limitations such as egos, forgetfulness, stubbornness, etc., and personal politicking.
A blog by Pardhasaradhi Reddy Chelikam on the SAP website summarizes the obstacles of digital transformation as follows:
- High capital investment
- Business model adaptation
- Unclear ROI (Return on investment)
- Lack of adequate skill set to expedite the transformation towards I4.0 functionalities
- IT security issues (Letting critical process networks open)
- Reliability/stability of communications between machine-to-machine/user interfaces
- Reluctance to change management
- IT system outages/failures that would cause huge re-investment
Moving Forward with Industry 4.0
The most common obstacle verbalized is that business is too hot and the human resources are too few. This means that still, so many have not even invested enough to arrive at the above-cited objections. But this trend is changing, as Tim Heston noted in the December 2022 issue of the Fabricator. The focus is shifting from capacity and capability, towards reliability and efficiency.
So, we’ve gone over the background, history, importance, and obstacles of Industry 4.0. But how do you overcome those obstacles to embrace the idea of a smart factory? It starts with examining what’s within your reach and control.
In the next segments of this blog series, we’ll cover why data matters in Industry 4.0, and what kind of data to start tracking. Stay tuned and subscribe to our blog for more on this.
Sangiacomo Presses Americas is ready to help you optimize your stamping press operations with our adjustable stroke press.
Learn more about our stamping presses by visiting our main website here.
Still considering your options? Our helpful sales reps will gladly answer any questions or concerns you have.
Contact us today at 256-275-4701 or email us at info@sangiacomo-presses.com.
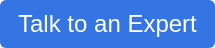